Metal Alloys
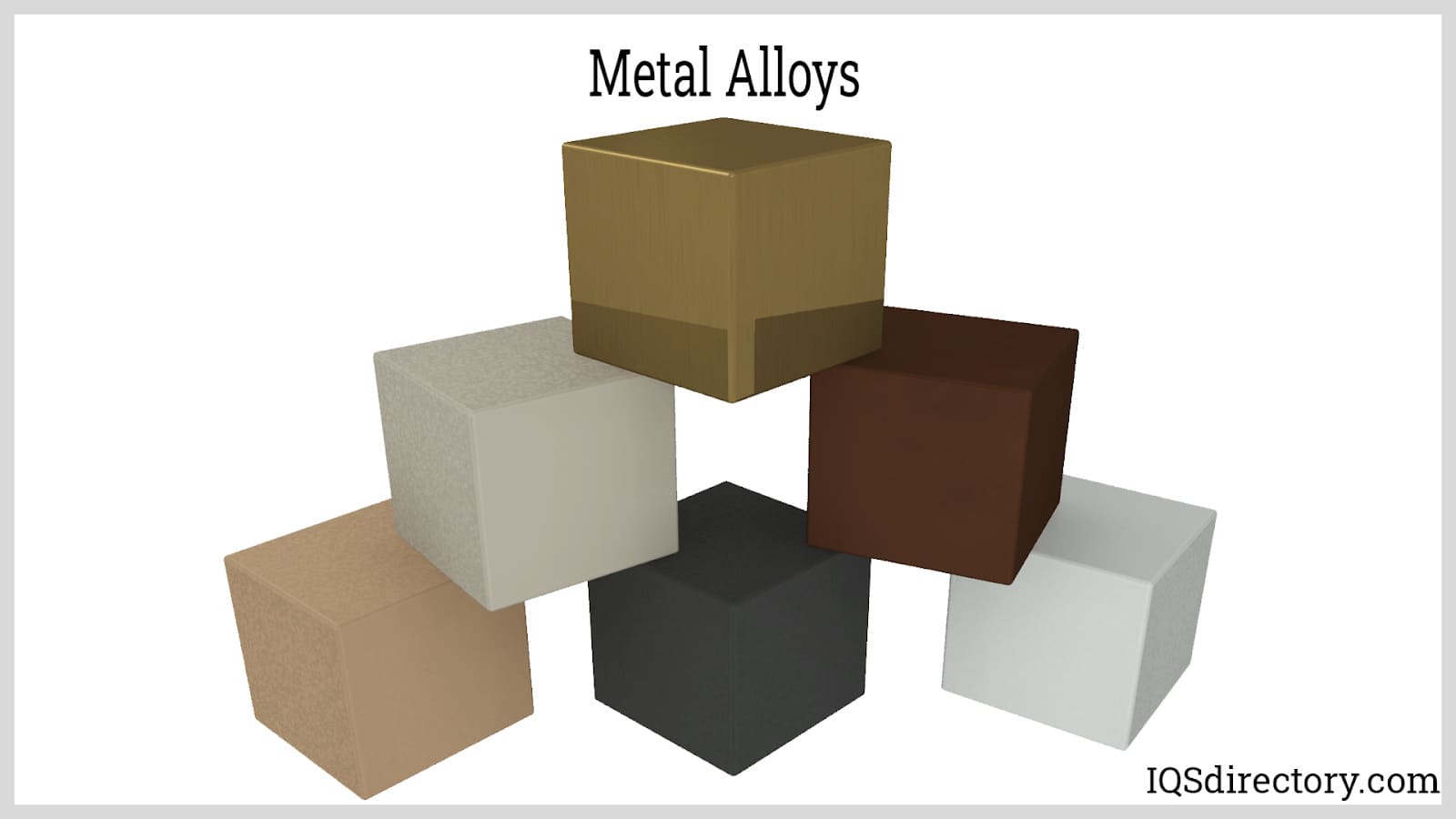
In modern manufacturing, the majority of products rely on metal components for support, structure, and containment. The versatility of metals—capable of being molded, shaped, and customized to fit any application—has cemented their status as indispensable in today‘s production landscape. This intricate process hinges on the seamless collaboration between metal suppliers and manufacturers, ensuring that raw materials are readily available and expertly transformed into essential components.
When it comes to metals, defining them by a single type is nearly impossible. Most metals are alloyed, a process that enhances their resilience, stability, and strength. Rarely is pure metal utilized in production. Consequently, suppliers and manufacturers are perpetually seeking innovative ways to enhance their products through superior quality materials.
Understanding that most metals are alloys is essential. Simply put, an alloy is a blend of metals designed to enhance their positive traits and minimize their less desirable qualities. This alloying process imparts durability to many everyday products. The primary goal of creating alloys is to make metals harder, more corrosion-resistant, and more malleable, to increase their temperature tolerance, or to imbue them with characteristics that facilitate various manufacturing processes.
One of the most prevalent alloys is aluminum, a naturally soft metal that gains remarkable versatility when alloyed with stronger metals. Aluminum components are ubiquitous in homes, machines, buildings, and vehicles, appearing in roofing materials, window frames, doors, and decorative items. Designers favor aluminum for its adaptability across a wide range of applications. Perhaps its most familiar use is in aluminum cans, which are easily recyclable and a staple in everyday life.
While aluminum boasts an impressive appearance, copper is another versatile soft metal with a wide array of applications. Copper’s utility is enhanced when alloyed with tin or zinc to create bronze or brass. Copper and its alloys are celebrated for their aesthetic appeal and resistance to rust and corrosion. They are particularly favored in wire production due to their soft texture, exceptional conductivity, and ease of extrusion. Additionally, copper is highly esteemed for its use in piping, offering both reliability and durability in various settings.
Among the myriad manufacturing alloys, stainless steel stands out as the most widely used for producing a vast array of products. Since its discovery in 1913, stainless steel has become integral to nearly every industry that relies on metal. From airplanes and automobiles to cookware and construction, stainless steel is prized for its exceptional resistance to rust and corrosion, as well as its strength and durability. Its versatility and reliability make it indispensable across various sectors.
Although alloys dominate the world of metals, the natural element nickel stands out for its remarkable attributes. Found in nature typically bonded with iron, nickel is celebrated for its exceptional malleability, ductility, heat resistance, and durability. Additionally, its ferromagnetic properties and resistance to rust and corrosion further elevate its status. When combined with metals like chromium, iron, and copper, nickel‘s versatility is significantly enhanced, amplifying its inherent qualities and broadening its spectrum of applications.
Titanium and tungsten, both naturally occurring metals, possess properties akin to those of nickel. When these metals are alloyed with steel, iron, or aluminum, their inherent characteristics are significantly enhanced, resulting in superior resilience. Similar to stainless steel, titanium and tungsten find diverse applications, ranging from the creation of exquisite jewelry to serving as vital components in spacecraft construction.
Alloys are sophisticated metallic composites crafted by blending metals with other elements to fine-tune their properties. This process is employed to achieve a range of enhancements, such as increased hardness, improved corrosion resistance, enhanced malleability, greater temperature tolerance, and optimized manufacturing capabilities like extrusion and die casting.
These alloyed metals serve a multitude of purposes across various industries. They are integral in the production of pipes, machine stock, and high-strength structural components for buildings and equipment. Additionally, they’re used for functional and decorative architectural elements, jewelry, appliances, tools, electronics, and even currency.
Alloy suppliers provide metals with enhanced strength, durability, and other desirable properties, surpassing those of their individual components. These alloys, including aluminum, copper, magnesium, steel, and various non-ferrous metals, exhibit superior material characteristics, making them highly sought after in the market.
However, the engineering properties of alloys, such as tensile and shear strength, can differ significantly from the original materials. These base metals might have been more heat-resistant and less brittle under certain conditions. To address these variations, lightweight alloys with strong heat resistance, known as high-temperature alloys, are developed. These alloys, composed of two or more metallic elements, can withstand extreme temperatures, such as 2000°F (1093°C). Superalloys, a subset of high-temperature alloys, offer additional benefits, including increased mechanical strength, excellent surface stability, and resistance to both corrosion and oxidation.
A wide range of metals can be used to form alloys, resulting in a diverse array of options, such as stainless steel, pewter, brass, bronze, and specialized custom alloys. Custom alloys are chemically modified to meet specific application requirements. Additionally, alloys are categorized based on their utilization in various processes, such as brazing alloys and welding alloys.
Learn more about alloys.
Aluminum and its versatile alloys can be transformed into an array of forms to meet the diverse demands of numerous industries. These forms encompass bars, coils, plates, tubing, sheets, strips, wires, rods, and pipes. Such products find essential applications across a broad spectrum of sectors, including architecture, chemical processing, defense, automotive, aerospace, transportation, marine, and food and beverage industries, among others.
In the realm of architecture, aluminum proves indispensable, serving in the construction of siding, roofs, windows, and doors, while also providing an insulating layer to buildings. In the intricate world of chemistry, aluminum emerges as a key component in antacids. Its versatility extends to the aviation and defense industries, where it is a fundamental material for aircraft wings and military vehicles. Aluminum‘s presence is equally vital in the production of irrigation pipes, automobiles, transport cables, and overhead power lines.
On the industrial front, aluminum is the backbone of beverage packaging, found in beer and soft drink cans. Within the domestic sphere, its utility is evident in everyday items such as food storage foil, pots and pans, cooking utensils, and various household appliances.
Learn more about aluminums.
Aluminum extrusions, celebrated for their impressive strength-to-weight ratio and cost-effective production process, are indispensable in a wide range of structural applications. These linear aluminum products, formed through either hot or cold extrusion, are shaped via dies into various profiles, including angles, beams, channels, and tubing.
The unique combination of strength and lightness makes extruded aluminum products ideal for numerous structural purposes. They find applications in light poles, building and window frames, lighting fixtures, car bumpers, hardware joints, trim, and many other construction, industrial, and automotive uses. Extruded shapes and channels can be crafted with precision tolerances, allowing them to interlock with other aluminum structures or function as heat sinks for cooling electronics, refrigerators, and heat engines.
Aluminum‘s inherent properties—strength, resistance to rust and temperature fluctuations, ease of fabrication, and complete recyclability—make it the preferred choice for building and structural materials. The versatility and reliability of aluminum and its alloys ensure that aluminum extrusions remain a top selection for engineers and builders alike.
Learn more about aluminum extrusions.
Copper, a versatile metal, plays a pivotal role in manufacturing a myriad of products. Its extensive use stems from its remarkable properties, such as exceptional heat and electrical conductivity. Additionally, copper‘s ductility allows it to be easily molded and drawn into wires, making it indispensable in electronic devices and wiring. Beyond electronics, copper finds application in various forms, such as tubes, sheets, and strips, in air conditioners, refrigerators, automotive parts, cookware, and lighting components.
Copper‘s versatility extends to its ability to form valuable alloys, with brass and bronze being the most notable. Brass, renowned for its muted, buttery yellow hue akin to gold, is typically composed of 67% copper and 33% zinc. The proportion of zinc influences the brass‘s color, with higher zinc content yielding a lighter shade.
Bronze, another prominent copper alloy, competes closely with brass in popularity. The copper content in bronze varies significantly, ranging from 60% to nearly 90% in some commercial grades. Tin is the second most prevalent element in bronze, constituting between 12% and 40% of the alloy, further enhancing its properties and applications.
Learn more about coppers.
Magnets, typically composed of metallic alloys—often including iron—generate a "magnetic field" that draws other magnetic objects towards them, while simultaneously attracting or repelling other magnets. They come in various forms, each distinguished by its magnetic strength, heat resistance, corrosion tolerance, and permanence.
Magnets can be broadly categorized into two types: permanent and non-permanent. Non-permanent magnets, known as electromagnets, require an external power source to become magnetic. These electromagnets are vital in numerous industrial applications, including solenoid valves, AC and DC motors, biomagnetic separation, and transformers.
Permanent magnets encompass ceramic magnets (ferrite magnets), alnico magnets, and rare earth magnets. Ceramic magnets, for example, have lower magnetic power and are more brittle than other types, making them more prone to breakage. However, their cost-effectiveness makes them ideal for non-structural applications such as motors, magnetic chucks, and magnetic tools. In contrast, rare earth magnets, though more expensive to produce, offer superior magnetic strength and retention. These robust magnets are essential in industrial applications like holding and lifting, motors, speakers, sensors, testing, and MRIs.
Learn more about magnets.
Nickel, with its atomic number 28 and symbol Ni, is a naturally occurring chemical element often found in combination with iron (Fe) within the Earth‘s crust. This silvery-white transition metal, first isolated in 1751, has historical significance, being used in tools as far back as 3500 BC.
Nickel‘s enduring popularity stems from its remarkable properties: it is malleable, ductile, highly heat resistant, durable, ferromagnetic, and exceptionally resistant to rust and corrosion. These attributes make nickel indispensable across various industries, including military and defense, electronics, coinage, and industrial manufacturing.
In the military and defense sector, nickel and its alloys are crucial for fabricating rocket motor casings and missile components, among other applications. This versatility underscores nickel‘s critical role in modern technology and industry.
Learn more about nickels.
Stainless steel, a remarkable category of steel, stands out for its exceptional resistance to corrosion, rust, and staining. Its unique properties stem from a significant chromium content, with a minimum of 10%, which imparts its renowned durability and resilience. By adjusting the levels of chromium, nickel, and molybdenum, various types of stainless steel can be created to suit specific needs.
Renowned for its longevity, minimal maintenance requirements, and full recyclability, stainless steel is an exemplary material for a vast array of applications. From the smallest components to large-scale structures, its versatility is unmatched.
Steel service centers offer an extensive range of stainless steel products, including foil, wire, strip, bars, plate, coil, sheets, and rods. These materials are crafted through hot rolling and forming processes, ensuring they meet diverse industrial and commercial needs.
Stainless steel is indispensable in manufacturing a wide variety of products, from kitchenware and tableware to electronic appliances and laundry equipment. It also plays a crucial role in sinks, kegs, vats, silos, and large kitchen installations. Its application extends across numerous industries, notably engineering and construction, where it is used in everything from elevator doors and gutters to the towering skyscrapers that define city skylines.
Learn more about stainless steel.
Stainless steel tubing, often abbreviated as SS tubing, stands as a versatile and essential component across numerous industries. With its hollow, cylindrical design, SS tubing and pipes are indispensable for transporting gases and fluids, as well as serving as integral parts of complex machinery and systems.
Renowned for its corrosion resistance, strength, and impeccably smooth, crack-free surface, stainless steel tubing has spurred the development of various specialized forms. These include corrugated stainless steel tubing, which is flexible and features a protective PVC outer layer; stainless steel pipe fittings, essential for connecting pipes; seamless stainless steel pipe, known for its flawless construction; and stainless steel square tubing, a robust alternative to the conventional round shape, offering enhanced pressure resistance.
The ingenuity and reliability of stainless steel tubing continue to drive innovation, meeting diverse needs with unparalleled efficiency and durability.
Learn more about stainless steel tubing.
Steel service centers are specialized facilities that meticulously process and treat various alloys of raw steel, transforming them into high-quality materials for manufacturers. These centers cater to a diverse array of industries, including aerospace, automotive manufacturing, construction, electronics, and shipbuilding, among others.
In their operations, steel service centers produce a wide range of preformed shapes, such as steel beams, strips, tubing, and I-beams, alongside a multitude of pre-production treatment processes. Remarkably, around 70% of all steel acquired by these centers undergoes some form of pre-production processing. Services offered include steel galvanization, aluminization, hot rolling, and cold rolling, ensuring that the steel is ready for use in the creation of various steel goods.
Learn more about steel service centers.
Titanium, derived from its eponymous element found abundantly in nature albeit not in pure form, possesses a remarkable array of inherent qualities. Renowned for its ductility, efficient heat conductivity, low density, exceptional strength, and robust resistance to corrosion, titanium finds diverse applications across several industries. It is indispensable in aerospace and marine sectors, automotive manufacturing, surgical and dental procedures, competitive racing, fine jewelry craftsmanship, and aquarium construction. To optimize its inherent properties, titanium is often alloyed with metals such as steel, iron, or aluminum, resulting in composite materials that combine the best of both worlds.
Learn more about titanium.
Tungsten, originating from the Swedish "tung" and "sten," meaning "heavy stone," occupies the 74th position on the periodic table. Renowned as the heaviest practical element, tungsten is one of the most thermally resilient metal currently recognized. Furthermore, in its pure form, tungsten exhibits the lowest vapor pressure among all non-alloyed metals, underscoring its exceptional stability and utility across various industrial applications.
Moreover, tungsten and its alloys are prized for their elevated density, formidable tensile strength, superior corrosion resistance, and outstanding electrical and thermal conductivity. These exceptional properties render tungsten highly sought-after across a spectrum of industries, encompassing consumer goods, construction, electronics, electrical applications, lighting, engineering, industrial manufacturing, jewelry, mining, and medical equipment. Tungsten has an indispensable role in diverse technological and industrial sectors worldwide.
Learn more about tungsten.
Wire rope, an engineering marvel born from the depths of 19th-century German mines, intertwines multiple strands of wire filament, each meticulously twisted together and helically wound around a robust core. Evolving from its humble origins, wire rope has cemented its role as an indispensable asset across diverse heavy industries. From the rigorous demands of mining and oil rigging to the intricate needs of bridge construction and marine operations, its versatile strength and reliability have made it the cornerstone for lifting, supporting, and securing applications, including the modern elegance of cable railings.
Manufacturers and distributors discern wire cable variations by detailing the number of strands and wires per strand, ensuring clear comprehension of their strength for all purchasers. Additional categorizations based on length or pitch provide further clarity. Advanced identification codes delve deeper, revealing core type, weight limits, and other critical details. Accompanying hardware such as connectors, fasteners, pulleys, and fittings are meticulously cataloged, showcasing a spectrum of strengths and fray-resistant capabilities within the same comprehensive framework.
Learn more about wire ropes.